Ep103: Dr. Silvia Madeddu "Industrial Heat is Electrifying!"
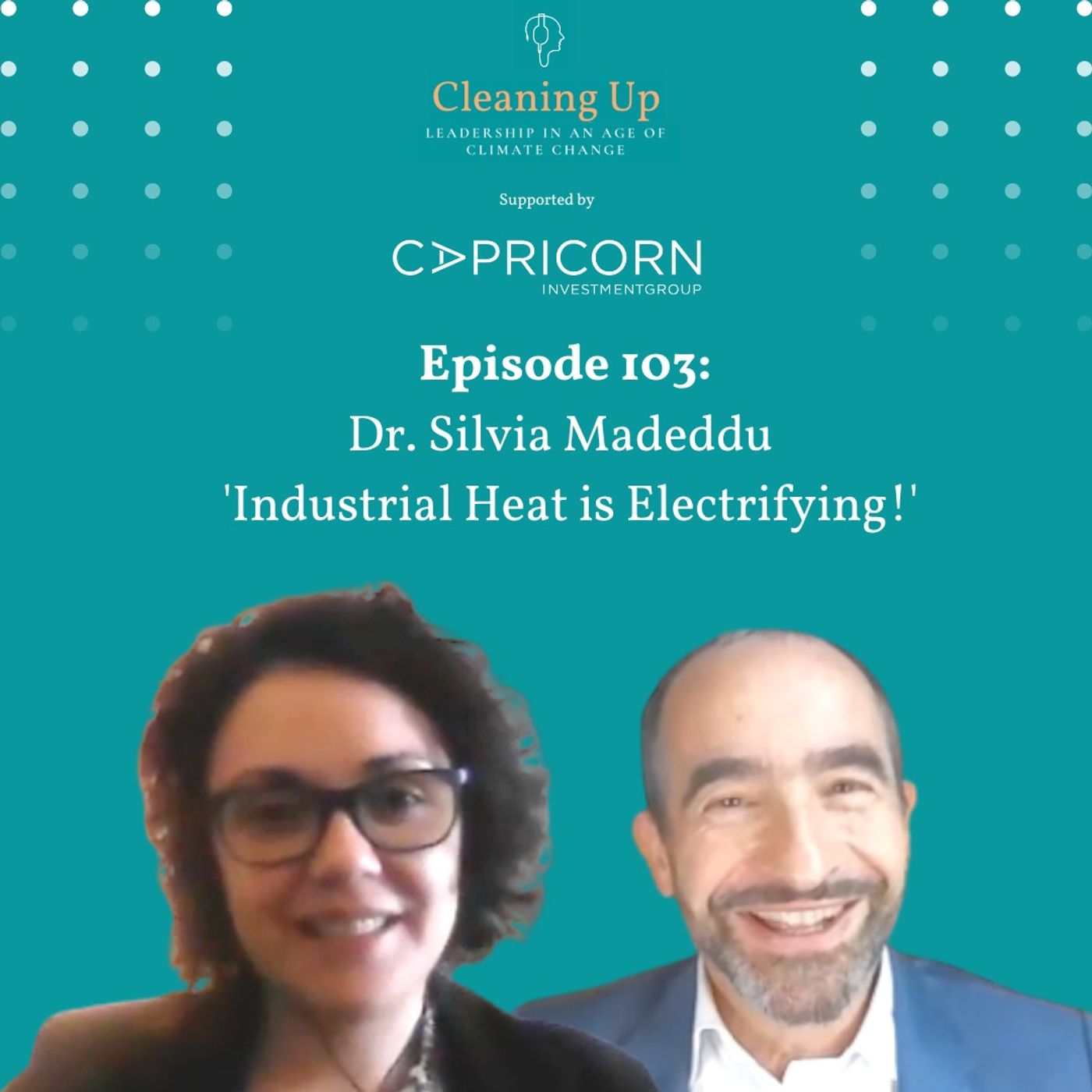
Dr Silvia Madeddu is a scientist and expert in decarbonisation strategies for energy-intensive industries. Dr Madeddu has a particular area of expertise in industrial heat, and is at the cutting edge of research hoping to transform the energy transition in Europe and beyond.
Dr Madeddu is Senior Sustainability Consultant at Schneider Electric as of August this year. In her previous role, Dr Madeddu was part of the Global Energy Systems modelling group and was Senior Scientist on Industry Decarbonisation at the Potsdam Institute for Climate Impact Research (2018-2022). At PIK, she helmed research into the potential of direct electrification of heat supply for reducing industrial CO2 emissions.
Prior to joining PIK, Dr Madeddu served as Chief Scientist at Cambridge Carbon Capture, developing new Carbon Capture and Utilisation (CCU) technologies. Dr Madeddu holds a PhD from the University of Sheffield in Materials Science and Engineering, and a master’s in Science and Technology from the University of Padua.
Click here for Edited Highlights
Michael Liebreich Before we start, if you're enjoying these conversations, please make sure that you like or subscribe to Cleaning Up. It really helps other people to find us. Cleaning Up is brought to you by Capricorn Investment Group, the Liebreich Foundation and the Gilardini Foundation. Hello, I'm Michael Liebreich and this is Cleaning Up. Now most of my guests on Cleaning Up have spoken about the decarbonisation of the electrical system through renewables or nuclear. They've talked about decarbonisation of transportation, decarbonisation of heating, domestic, offices, commercial heating. My guest today is Dr. Silvia Madeddu, and she is a great expert on the decarbonisation of industry. She was the Senior Scientist on the decarbonisation of industry at the Potsdam Institute, and recently became Senior Consultant at Schneider Electric on sustainability. Please welcome Dr. Silvia Madeddu to Cleaning Up. So, Silvia, thank you so much for joining us here on Cleaning Up.
Dr Silvia Madeddu Thank you, Michael, thank you for inviting me.
Michael Liebreich Now, where are you calling in from? You've got a sort of blurry background there; I get no visual clues at all.
Dr Silvia Madeddu So, I'm on the Baltic Sea, in the north of Germany. And I'm normally based in Berlin. But today, it's a long weekend, so I'm here for holidays, and I'm recording... I'm based in this touristic location on the Baltic Sea.
Michael Liebreich Thank you very much for interrupting your long weekend to be with us here. What I'd like to do is if I could, if I could start by asking you kind of in your own words, what it is that you do and who you are? Because, I came across you because of your extraordinary work on industrial heat and the electrification of industrial heat. But give us a very sort of short overview of your bio?
Dr Silvia Madeddu Yes, so normally I work as an expert in industry decarbonisation strategies, and right now I work for Schneider Electric. I'm part of the sustainability business team. And I work as a senior consultant on sustainability topics. So, my everyday job consists of supporting these companies in assessing their carbon footprint, and also advising them on best practices on how to decarbonize their businesses. And before joining Schneider, I worked for four years at the Potsdam Institute for Climate Impact Research. And you might be familiar with my work. We published this study, which I think to my knowledge is the first technical assessment on the feasibility of industrial electrification.
Michael Liebreich And, of course, from the Potsdam Institute, we had Johan Rockstrom was one of my.... I'm not supposed to have favorite episodes, but that was one of my favorite episodes, talking about the planetary boundaries and the sort of time dimensions between when we need to act, and then when the really bad impact of climate change might happen, and how long feedbacks might take and so on. And he was very brilliant. So, he was the Director of the institute.
Dr Silvia Madeddu Yes, yes. He's co-directing the institute right now, yes.
Michael Liebreich But now tell me I think of Schneider Electric and, you know, the audience for Cleaning Up, they're very knowledgeable, overall, but they may not be familiar with Schneider Electric; I think of them as being largely around electrification and digitization, particularly around the digital control of the energy system. Is that fair? Or is that not fair?
Dr Silvia Madeddu So, Schneider Electric is a leading company on digitization. So, what they do is they support companies in Process Automation. But they have many different hubs, many different teams. So, they also work a lot on energy management, energy efficiency. So, these measures are in a way connected to if we're going to talk about digitalization, process automation, management. I think they all go hand in hand with electrification first. But then, yes, personally, I'm part of the sustainability business team. So, Schneider Electric has now this consultancy hub, where they try to support these companies in starting this journey of submitting, for example, science-based targets, assessing their carbon footprint. This is very interesting because what we see is a lot of companies are searching for this type of opportunity. Because it's very, very challenging to estimate carbon footprints for companies like multinationals, for example; they have business all around all around the world. And what people might not know is that, when they assess their carbon footprint, they don't only have to account for what they produce in terms of emissions, but they also have to assess indirect emissions. So, from the supply of energy, and even most challenging is the accounting of emissions from their supply chain. Because then what we ask our clients is to engage with their suppliers, understanding where the majority of these emissions are coming from, and challenge their suppliers. And so, this is all part of a process where companies challenge each other, right. So, it has to be an interactive process. If I have a supplier that is very carbon intensive, I might try to ask him to do something about it. Or I might just change my supplier, something like this. So, it is very, very challenging for these companies. And it is definitely exciting to see all the manpower, energy that goes into this process.
Michael Liebreich Okay. And that's what you're currently doing. And I think we'll get back to that later in the conversation. But I want to just wind back to where I first became aware of your work, which was really around the potential for electrification in industry, and actually quite heavy industry. And you wrote this paper, you were lead author, I believe, on your paper. And it's one of those things that you know, the cliché is you always remember where you were when you heard about x. And I always remember the role that this paper played for me, in giving me the confidence to think about electrification of industry in a much more comprehensive way. Because your findings, if I paraphrase, were that actually much more of industry can electrify than we probably were calculating at the time. Is that a fair sort of top-level synopsis? Then we'll get into some of the sectors?
Dr Silvia Madeddu Absolutely, yes. So, I think the novelty of the study is first of all, when we think about electrification, we think of electrifying the transport sector through electric vehicles, and we think of electrifying the residential sector with heat pumps. And then here comes industry and people have very vague ideas or they provide normally multiple solutions for decarbonizing that sector. And I have to say that electrification until maybe when I wrote my paper, there was not much talk about electrification of industry, to be honest. And there are many, many reasons for this. And the first one is that normally industry is considered a hard to abate sector. And when they talk about why industry is considered hard to abate sector, they always mention that industry relies on fossil fuels, which in my opinion... of course, it's true, but it is not less than for other sectors. It's not that transport was not relying so much on fossil fuels or residential is not relying on fossil fuels. So, the reality is that industry relies on fossil fuels for different purposes. So, you they use fossil fuels for heating, and they use fossil fuels as raw materials for their processes. And so, that's why industry is always so hard-linked to fossil fuels. So, by thinking of the reliance of industrial on fossil fuels... 70% of the energy demand from industry comes from fossil fuels, and it's all used for heat purposes, or the majority of it is used for heat purposes. So, we thought okay, the best way to decarbonize that sector is to decarbonize its energy supply. And so, considering that electricity provides only 20-25% of energy to industry and the remaining is fossil fuels, we want to tackle the fossil fuels.
Michael Liebreich And the thing that I usually hear about this stage when I've tried to explain this is, 'oh, no, but we're talking about high temperature heat.' And that really can only be delivered by gas. And I hear this all the time, you've probably heard it also 1000s of times.
Dr Silvia Madeddu This is also something that was very surprising to me, because actually, we have plenty of electric technologies that can supply heat to very high temperatures, temperatures that are even higher to those that industry needs in their normal processes. So, industry normally needs temperatures up to 2000 degrees. Very rarely, they will need temperatures above 2000 degrees Celsius. And electric technology can go way above this temperature range. So, we don't have any problem in terms of the temperature that electric technology can reach. There is induction, there is resistance, there is electrical furnaces or plasma torches - they all go above 2000. Then we have other technologies that go above 1000 like microwave and infrared heating. Now, what I highlighted in my study is that the problem of these technologies is that so far, in some cases, not in all of them, but in some cases, they were applied to very specific processes. For example, electrical furnaces are mostly used to produce steel. Induction is used for melting metals, and then we have plasma torches in very, very niche applications, like for example, welding. So then, I wanted to understand why it is, why we didn't use electric technologies more in industry. And so, I also contacted some manufacturers of gas and electric furnaces, and I asked, okay... I was trying to understand what is their market, and what they said is that, well, we can produce an electric furnace that is as large as a gas furnace used in industry, that can be applicable to an industrial process. But the problem is that we don't have demand for this type of furnace, because industry would spend too much in electricity bills, and they prefer to use gas. And so, it seems to me that it was not... it's not an engineering problem. It's not that scaling up these furnaces, electric appliances, is an engineering problem. It's more, I don't have demand for it, so I don't have a market for it, so I don't produce the furnace. And by not producing the furnace and not implementing the furnace in an industrial process, I also don't improve the technology. So, I don't have the opportunity to optimize the technology to make it more efficient to integrate it better in an industrial context. So, we see that these appliances sometimes have very niche applications. So, that was what I found out.
Michael Liebreich Okay, so that's kind of the first takeaway, hopefully, for the audience from this conversation: that there is no shortage of electrical technologies that can get to very high temperatures. The way I usually answer the question is, look, we do arc welding, so of course, they can get to high temperatures. But in your paper, table 1, and we'll put a link in the show notes, you go through a whole list of technologies, electrical technologies, that can get to very high temperatures. And so, what you're saying, though, is that so far, they've not been used, because they are more expensive, or at least there's the fear that they will be more expensive than natural gas, correct?
Dr Silvia Madeddu Yes, correct. First of all, let me specify that this study is based on the European industry. So obviously, I'm talking about the European context, right. And so, these technologies are used in industry, for sure. Like you just mentioned, welding. But if we want the electrification of industry to increase, we need to spread more electrification, it has to penetrate more within the industry. So, we will have to use these technologies for many other processes and more extensively. So, that's what I found, exactly, that for industry today, on average, in Europe, the electricity cost is three times that of gas. Well, these are numbers before this energy crisis... And so, it is very expensive to power a process with electricity, which in a way, it's contradictory, because we know that renewables are the cheapest energy source that we have today. So, the cost that we have today in our electricity in Europe, is due to many factors, huge taxes and levies, but also the fact that obviously, we don't have still that capacity of renewables in our grid.
Michael Liebreich Okay, now we're gonna get on to what happens now, what happens next. Because of course, if you compare electrification to natural gas, it's not just that there's a price difference, there's also an emissions difference. So, if you say, well hang on a second, now we need to get off the natural gas or we need to capture the carbon or something, then the cost of that is going to go up. And we'll talk a bit about where that ends up. Before we do though, I just want to talk about the lower temperature heat. Because when you're talking about food processing, in this country, when you talk about something like making whisky, where the heat is needed to boil off alcohol - I don't know the temperature, I think it's something like 70 degrees, plus or minus - what is the role within your work of heat pumps for those lower heating temperatures? Is that just a complete no brainer? Or there are good reasons why we shouldn't do that?
Dr Silvia Madeddu Um, no. Well, we should first of all specify what we mean by low and medium temperature. So, it depends, many people would consider medium temperature up to 400 degrees. If we identify a temperature range from up to 200 degrees, this would be also low and medium. But let's think about the heat supply up to 200 degrees. So, heat pumps could play a very important role for industry, given that they are capable of supplying heat up to 200, which right now is not still possible, and steam. And this is the other question. So right now, we want heat pumps to supply steam, this is the new frontier. And when I wrote my paper, I'm very happy to say this, my paper is already old news, because when I wrote my paper, I considered operating heat pumps until 100 degrees. And I mentioned that there is a limit in the pressure of the steam that they can supply because there was a limit at that time of three bar. At least this was my knowledge. So, my study excluded heat pumps from the steam supply, and from all the heat supply above 100 degrees. Now there has been incredible, but really incredible, astonishing, development in heat pumps in only in the past three years. So right now, I was researching right now what is the temperature limit of heat pumps at the moment, I found that there are already commercial heat pumps that are supplying heat at 160 degrees. They can supply steam up to six bar, at least these are the examples I found, and maybe there might be even more performing heat pumps. But this is an incredible, incredible development. And I'm talking about right now because obviously, there are always the mechanical vapour recompressors that are also a sort of heat pump. But I'm talking about a heat pump like the closed loop or the open loop that are not classified as a mechanical vapour recompressor. So, there has been huge development. So obviously, I would have to really rewrite part of my paper to include these novelties.
Michael Liebreich What about if you look at... is there a theoretical limit? Because, you know, heat pumps producing steam... There may be people out there who are not excited about that, but for those who can see behind me Fermi's Thermodynamics, I get terribly excited about that because the potential, the steam market, is absolutely huge. And if you're now including that into heat pumps, then quite clearly that's a game changer. How far could it go? What temperatures and pressures are people achieving in the lab or the research environment?
Dr Silvia Madeddu I think right now we the research that is going on right now is targeting temperatures above 200 degrees. Above 200 degrees, I know that there is the Danish Technological Institute, I think they are working on developing such a heat pump, that would operate above to 200 degrees. And in terms of pressure, I'm not sure. But right now, we can definitely supply six bar which is already a huge improvement on what it was three years ago. And steam heat pumps that supply steam exist, and they are commercial, and they can be operated in industrial areas, industrial plants.
Michael Liebreich And those temperatures open up the food industry, they open up the textiles industry, they open up lots of demand for heat that is in that... let's call it up to 200 degrees. That's a lot.
Dr Silvia Madeddu If we cover up to 200 degrees, then it's more or less 37% of the demand from industry. So, it's a huge, huge scale opportunity. And it's a huge opportunity to decarbonize industry, and not only to make industry more efficient, because let's not forget that heat pump is the most efficient technology that we have to electrify industry right now.
Michael Liebreich Silvia, let's come back to the question of efficiency, because I want to do some slicing and dicing on that between the primary use and then the final, useful energy efficiency. I think it's very important that we get to that. But give us the percentage findings of your paper. So, that was even before you understood that heat pumps could get up to delivering steam, so when you had them going up to 100 degrees, you still found some incredibly striking findings.
Dr Silvia Madeddu Yes. So, we found that... Well, first of all, in the paper, we have three different stages of electrification. So now I give basically the range that we identified from between stage one and stage three. So, with mature technologies, we found - so technologies that we have today, we don't have to reinvent the wheel or we don't need rocket science - technologies that are already mature and existing, we could, we can electrify industry up to 78% of its energy demand, which is, like you said, quite...
Michael Liebreich Silvia, can you distinguish between feedstock... because I know that there is always this confusion between... you may be using some of the natural gas to make fertilizer, but that's not the heat demand of that sector. So, can you just distinguish... your 78%, is that of the heat or is that of the use of fossil fuels in all of those sectors?
Dr Silvia Madeddu So, you're correct. So normally in industry, in my paper we included the feedstocks, but now, the feedstock, maybe you're not familiar with this, fossil fuels are used as raw materials in the chemical industry. And they account for quite a large chunk of the energy used in the European industry, but, excluding those that are not obviously heat, they are not consumed to supply heat. So, they are not a form of energy that we can directly substitute with electricity. So, forgetting the feedstocks, and considering only the energy demand beyond feedstock, then we could electrify between 66% In the first stage, and 78% in the second stage, which includes only mature technologies. So, it is a huge electrification potential that we identified. Of course, we also identified of this 78%, there is still some percentage, and these we identified are the technologies that are not yet developed. So, that are still in a development phase; I didn't find really an indication that these technologies are used in industry today, so they are excluded from the 78%. But if we were to include these technologies that today are currently under development, meaning that there are demonstration plans, these technologies are being piloted, so it's not that we don't know what they are, I mean, they are there, but we are still testing them. Then the potential would increase to 99%. So, huge, huge potential.
Michael Liebreich Which is essentially all industrial heat. And when you say that these are not mature, I mean, this is not breaking any new ground in terms of physics. This is just saying, there is no manufacturer currently of a machine to do X that uses electricity? They're all currently using gas.
Dr Silvia Madeddu Exactly. So, what I was trying to, obviously, find examples of... So, first of all, let me mention what are these technologies. These technologies are steam crackers, that are used in the chemical industry, and then in clinker making in the cement industry. So, I didn't find application of electric technologies that are actually being operated by a big chemical producer or cement producer. But at the time, I could only identify two projects, one for this electric cracking and one for the electrification of clinker making. And today, I can already say that, again, this is old news, in the sense that there are at the moment, several projects ongoing, that are trying to demonstrate at industrial scale these technologies. There are many projects, not only one. And this is for me something that three years ago was not there; I could only find one example for each. And now there are at least three examples for each. And these are also big players in the chemical sector and the cement industry. So, it means that industry is starting to feel the need to develop these technologies. And they're also seeing the opportunity, right. So, to start electrifying these processes.
Michael Liebreich One example that I saw recently was metallurgical treatment - so heat treatment of steel - that would all have been done using gas. And now there's a big pilot, one of the big manufacturers has been investing in electrification. So, electric furnaces to do heat treatment of steels. Is that the sort of thing that you're now spotting more and more coming along?
Dr Silvia Madeddu Absolutely, yes. First of all, steel, electrification of steel, what I found in my study is that all those processes that are not related to the reduction of the iron ores - so, they need a reducing agent, that obviously cannot be... I mean, it can be electrified, but it's in a very early stage. Anyway, we're identified that more or less 30% of today's demand could be electrified with existing technologies. Then we have the secondary steel production, which is already fully electric. And so, this obviously could be expanded, although there are limitations in the availability of scrap. I think that still is one of the sectors that to be decarbonized we need indirect electrification, so it will need the usage of hydrogen, because this is today the best alternative we have for reducing the minerals, at least. But there are still 30% of energy using steel that is not related to reducing iron ore that can be electrified, with, like you said, there are induction furnaces, resistant furnaces, electric car furnaces for the secondary steel so there is potential. And there is also a pilot, a project - the BAMBOO project - that is gonna test the implementation of a heat pump in the steel industry. So, also something that we normally don't think of heat pump supply to high temperature industries. It's still happening. So, there is potential for electrifying steel for sure.
Michael Liebreich So, let me just focus on steel for a second. So, you've got this kind of 99% of industrial heat that could go electric. Does that include electrification of steel because it's through arc furnaces using steel scrap? How do you deal with primary steel production? Because there are ways of doing that electrically, but we're not sure if they'll work? So, the Boston Metals process.
Dr Silvia Madeddu So, what I did in my study, my study was focusing on direct electrification. So, I was not looking at indirect electrification. But I do obviously mention the fact that today, we have different ways to electrify steel, directly and indirectly. When we talk about the main, the core of the steel production, which is we want to get rid of the reduction of ore in blast furnaces; they use a lot of coke, which is a derivative of coal. So, what we assumed is that all the primary still gets substituted by secondary steel production. Because we know today that there are circular economy studies that show that we have enough steel that is currently in use that eventually we saturate the market and will be available to be used and produce secondary steel. But obviously, it's a study that is looking at the stock use of steel. So maybe steel production in real world terms will continue to increase. And so, it is probable that we will not be able to substitute all the primary production with secondary steel production. And in any case, in use steel stocks will be available with time, but maybe you know, there are developing countries, that will consume a lot of steel in the next 10 years. And we cannot ignore these countries. And so, the point I make in the paper is okay, if we have this in use stock steel, we can really produce enough steel only by the secondary method, so using the electric arc furnaces, so electrifying fully the steel. But it is more likely that we will need alternative solutions to decarbonize the primary steel. And in this sense, I think that there are two ways. One is the hydrogen route - so we produce hydrogen from renewables and we use this hydrogen as a reducing agent. So, what the carbon is doing in the current process, we substitute with hydrogen. The other method, like you said, I don't know if you're referring to the electrowinning process, using only direct electrification process, so it uses electricity to strip the oxygen out of the iron. But it is still at a very early stage. And so, the timing is important in the decarbonisation of industry. So, I think that we have, we cannot exclude the hydrogen route for the decarbonisation of steel.
Michael Liebreich Right. So, I just wanted to clarify because 99% is very high. But it's so high partly, I guess, because this is a European study where it's conceivable to think that we could survive on secondary steel use, on recycling. Whereas if this was a China Study, you would have to say, well, actually, given that electric reduction of steel is not yet proven, that would have to be outside the mature technologies piece of the work. If I'm if I'm paraphrasing correctly?
Dr Silvia Madeddu I think, I hope in the paper it's clear enough that for me that direct electrification of steel, full direct electrification of steel, it is something that might come but maybe much later on. And so, right now, we need a solution today to decarbonize steel. And this in my opinion is definitely hydrogen. Then of course, like I said, there are other thermal processes in steelmaking that are not related to the chemical process. That is, the reduction of iron. But we have sintering and other thermal processes, casting etc. that can be electrified.
Michael Liebreich Okay. In a sense, that's a caveat around steel. There's also a caveat around these process emissions. So around cement, a big chunk of the co2 is the chemical process, which... You can still heat it all electrically, but you're still going to produce.... Until we change the chemistry of cement, we can't do anything about that. So, that's a bit of a caveat. Let's move on to this question of efficiency, and then we'll come back maybe to costs. Because what you also found, and again, this was, for me, an incredible sort of enlightening 'aha', was that once you go electric, it opens up routes to efficiency, that are not available when you're using gas. The way I describe it is, when you cook pasta on a ceramic hob, 90% of the energy goes into the water and the pasta. And when you do the same thing with gas, only 60%, and the rest goes into your fume hood, or into your room and it's lost. And so, you discovered similar things, did you not? Can you talk about the efficiency of processes comparing the gas route, the fossil fuel route to the electric route?
Dr Silvia Madeddu Yes. Well, first of all, you're absolutely right. So, in general, what we found is that electric technologies are either comparable, but more often, they are more efficient than gas-based, combustion based processes. So, there are efficiency gains that are associated with electrifying the industry. But the most obvious, like we already discussed, is the heat pumps, because they are the most efficient technology. So, to supply one kilowatt hour of heat, heat pumps consumed eight times less energy than a boiler. In this at least, we have a coefficient of performance of three, but there are heat pumps that can go above that. So, they are much more efficient than any boiler, either electric or gas-fired. So definitely, they gave us the best efficiency gains. Then, there are all the other technologies. So normally, for example, glass melting in, in a gas-fired furnace, has an efficiency between 40% and 50%. And all electric furnaces have an efficiency of up to 80%, 90%. So, huge efficiency gains. And yeah, so this is applicable to almost all furnaces. For example, induction melting, it's also super-efficient, especially because the heat gets directly into the material, so really small furnaces can go up to 95% efficiency. So, we really have proof that it would be very beneficial to electrify industry from the point of view of reducing energy consumption. There are also other benefits, for example, very interesting, you just mentioned the fact that cement has many process emissions that are coming from the from the decomposition of limestone. What is the problem today, if we want to capture these emissions is that the CO2 coming from limestone, that is fairly a pure stream of CO2, gets mixed up with the flue gases, because we put these combustible fuels within the kiln, and they get mixed up. So, if we had an electric kiln, that would calcinate the limestone, we would have a pure stream of CO2 from the limestone and we wouldn't have any other flue gas from the kiln because the kiln is electric. So, we would have a pure stream of CO2 that can be directly captured without needing to separate the CO2 and having these mixed flue gases within it. So, it would be a much cleaner industry. Not only that, with an electric furnace, or an electric appliance, you don't need all that equipment that you need today, when you have a combustion system in place to control the emissions level. There are afterburners sometimes, you know, to reduce the volatile organic compounds and so on. There are stacks that have to be installed, control systems for the emissions level, so many things that you wouldn't have when you have an electric furnace because it's a cleaner technology. And also, you would have no on-site emissions, most likely, because you get either electricity from the grid or you produce it yourself from renewables. So, you reduce your on-site emissions. So, there are many benefits in electrifying industry.
Michael Liebreich Did you look in that paper at the impact on something like air quality?
Dr Silvia Madeddu No, we didn't. And that's, for example, one aspect that one could consider. You would have much cleaner... Industry, on site you would reduce considerably emissions, so you don't have all those apparatuses and all those that you have you have combustion. Because with combustion, you are burning something that goes into the atmosphere.
Michael Liebreich To me this was a huge 'aha', the idea that you would improve the efficiency, reduce the energy need within the process. Because, you know, I am constantly trying to tell people that in this net-zero transition, we're not trying to replace the primary energy that we currently use, because two thirds of primary energy is thermal waste, from burning coal, from burning gas, from burning oil, and also a little bit of nuclear. But it's that thermal waste that we just don't need to produce if we go straight to hydro, solar, wind. And so, that's kind of like two thirds of the problem gone. But really, now you're saying within industry, there's maybe another... Did you come up with an average figure across those industrial sectors? Did you say we actually will reduce energy by 20%? What did you come up with?
Dr Silvia Madeddu So, we found that we would reduce energy input by between 5% and 20%. And I have to say that my paper is very conservative, because in many cases, in some technologies, if I didn't have figures for efficiency. For example, I don't know how more efficient would be a furnace that is used to electrify the clinker making, because this furnace simply today is not at an industrial scale doesn't exist. So, I was very uncertain on some efficiency levels, but we estimated - in a very conservative way I have say - that the efficiency input would be between 5% and 20%.
Michael Liebreich Of course, now, if steam can be made via a heat pump, well, that could then be that whole piece of industry could halve the final energy use or even more, maybe two thirds or 80%, depending on how...
Dr Silvia Madeddu Yeah. These figures are all old news because now we have heat pumps that can go way above that. And just to quote the figures, that was the outcome of this paper, the study, the amount of waste heat from industrial processes in Europe is 300 terawatt hours per year. And this waste heat can be directly fed to heat pumps, for example, to recycle this waste heat, reduce this waste heat, and upgrade it. So, it's a very huge potential.
Michael Liebreich There's yet more potential if you actually recycle the waste rather than losing it. And now, I said, we'll get back to costs, right? So, the problem is that this electricity, per unit of input energy, is three times natural gas, or at least it was before the current spike in gas prices driven by Russia's invasion of Ukraine and also the price spike that hit us at the end of COVID. But the correct comparison, is not electricity versus natural gas, or if it's natural gas, it has to be abated. Surely the correct comparison is electricity against hydrogen?
Dr Silvia Madeddu Yeah, I mean, in terms of hydrogen, I'm not so familiar with the cost of hydrogen right now, but I mean, I can imagine... Look, if we consider the process. So, we take electricity and we can use it directly right. And if there is electricity produced from renewables, we have no energy input, which we would have if we use for example gas to produce electricity. So, we have a clean energy source directly delivered to our industrial processes and get directly used with, like we said, very little efficiency losses, because electric technologies are very efficient. Now, when we talk about hydrogen production from I guess, clean electricity, what we have is production of electricity from renewables in theory, because we want to have green hydrogen obviously, then we transform this electricity into hydrogen through an electricity process. And then we have two options - we use the hydrogen directly or we produce e-fuels. So, for example, some hydrocarbon, so hydrogen, plus some carbon. There are huge efficiency losses in the production of hydrogen. So, for example, to convert electricity into hydrogen I think the efficiency is 70%. On top of that... we either use hydrogen directly, but if we use hydrogen directly, either we use it as to combine, for example, like in the ammonia process, or we combust the hydrogen. And then in combustion, we have other efficiency losses, because we just said the combustion systems are not at all efficient. If we produce e-fuels, we have another efficiency loss because we have to convert the hydrogen to the e-fuel, and then we have to take these e-fuels and combust them. So, overall, it's not an efficient way, not the most efficient way to use our clean electricity. But of course, when we don't have other options, we are forced to produce either hydrogen or e-fuels, but I would say that we should use directly electricity when we can, and then when we cannot, we can use the these fuels that are, these e-fuels for green hydrogen.
Michael Liebreich Cleaning Up is brought to you by Capricorn Investment Group, the Liebreich Foundation and the Gilardini Foundation. So, if you look at those two routes, direct electrification versus a hydrogen or e-fuels route, is it your sense that they will be cost competitive or that one will win or the other?
Dr Silvia Madeddu Look, I think that, in my opinion... the electricity price affects, obviously, the price of hydrogen, so in my opinion, direct electrification will be always more cost competitive. But obviously, like I said, there will be certain branches - I'm talking about industry, obviously, but then hydrogen obviously has other ramifications - but when I think about industry, there will be sectors where hydrogen will be the only solution, and so the price will depend on, you know, the other competing energy carriers, right? So, once we implement a certain carbon tax, or you know, fossil fuels become inaccessible... Right now, this energy crisis is showing that an energy carrier like gas, that we always considered as the most reliable energy source for the industry, is suddenly hindering the survival of many, many companies, right? Because energy prices are skyrocketing. So, in that sense, it is possible that hydrogen will become cost competitive in certain markets. But I don't see hydrogen competing on the cost directly with electricity, electricity that is produced from renewables, because renewables today are the cheapest energy source that we have, so.
Michael Liebreich I have this conversation, as you can imagine, quite often, and people say, oh, you know, hydrogen is going to become so cheap, that it's going to be the answer. But what people don't realize is, well, it comes from two sources, one is natural gas, which we've seen is risky, and so that may not be what you want to tie your strategy to. And the other is, of course, renewables; well, but if the hydrogen is going to be cheap, then the electricity is always going to be cheaper, the differential is going to remain the same. So, you have these slightly strange conversations. But there is something else though, which is that renewable electricity is intermittent. And a lot of these processes need continuous power. So, if you are making glass, you can't just make glass when the wind blows, and it's sunny, or if you are, you know, doing a process... a continuous furnace of some sort. So how do you square that circle? I mean, is that a good reason to say well, electrification, you know, this is all great, but actually, it's not going to work?
Dr Silvia Madeddu So, yes, you're correct. So, the big challenge for industry using renewables is exactly this. The industry can never shut down. Industry has, most of the time, continuous operations, and we need a very stable energy source. But for this, we have luckily available from storage, opportunities, energy storage opportunities, and today there are there have been huge developments in this field. We have had the development of these thermal batteries. For example, there is a company in the US that is developing these thermal batteries that absorb energy from renewable sources, and convert these into heat, and they can re-emit the heat at very, very high temperatures, up to 700 degrees, which would be sufficient, for example, for very high temperature processes, like I said, like those that I identified as very critical like clinker making. So, there are today... I'm quoting this company in the US that is producing these thermal batteries with bricks. But there are other companies in Europe also, for example, in Norway, that are developing the same. And there is a company in Germany, an aluminium producer, that has already developed this process, applying directly in its production process of aluminium, where they created a sort of a virtual battery, as they call it, which is basically giving flexibility to the industrial process through heat exchangers. And these heat exchangers work exactly like this, by balancing the energy supply and energy needs in these industrial processes. So, it is definitely possible to make industrial processes more flexible in the energy demand, but also to have storage technologies that are implementable in industry and supply the heat the industry needs. Just on this side, also very interesting for me, is that we need to think of industry, obviously, when we think of electrification, similarly to when we think about smart houses and smart buildings, or smart cities; we have to think of industry in exactly the same way. Industry will have to become a smart industry. So, load management, flexibility, etc.
Michael Liebreich Because I was already thinking that, you know, some proportion of industry is actually batch-processed. And of course, if it's batch processed, then it immediately lends itself to demand response, because you just... if the wind doesn't blow, you don't make a batch, you simply, do something else, maintain your machines, give everybody the day off, and then double the production when it is windy. But I don't know what proportion, I don't know if this is something you looked at in your research, what proportion of that energy demand is batch versus... It feels like much more would be continuous processes.
Dr Silvia Madeddu That's a good point, actually. But I think all the time when I talk with companies, all the time, their main problem, main issues is to keep their process continuous, ongoing, right, never shut down. So, I think that it depends also on the scale of the production, right? Probably companies that are very large scale production, they are continuous operations. And so, in this case, the flexibility is very important. And the storage opportunities become fundamental.
Michael Liebreich And I know that you are nervous about naming individual companies, but I can do that. So, there's companies like ENERGYNEST, there's Rondo in the US. There's Trimet and there's others working on load-following in aluminium. And, you know, we might put a few links into the show notes just for people who want to chase that up. But it's really about creating a buffer between the intermittency of the renewables, and then the continuous heat requirement, and something like Rondo, the temperatures they're looking at are not 700 degrees, I think they were looking at going up to 1200 degrees.
Dr Silvia Madeddu Really? I'm sorry, I wanted to say 1700 degrees. 1700, which would be sufficient to... to supply heat sufficient for clinker making, for example, up and around 1400 degrees. So, yeah, no, you're right, definitely higher.
Michael Liebreich Right. And, and that becomes, it just opens up so many different avenues if you do have that high temperature thermal storage, because then you can have your intermittent renewables, and you raise the temperature of something, some heat store, you keep it up there at 1700, or 1200, whatever the number is going to be, and it's much cheaper to store heat in ceramic bricks than it is in either electricity or hydrogen, I would suspect.
Dr Silvia Madeddu Yes, exactly. I think we consider always storage as something very expensive. But actually, the prices of the costs of storing energy in batteries, the price of batteries have decreased I think by 70%, in the past 20 or so.... There was a rebound last year, but the prices have decreased. So, we see also that any storage options, the cost of storing energy is always decreasing. Historically, it's true, we thought that storing electricity would be much harder. But thermal batteries are showing us that actually it's not, it is possible. And like you said with materials that we are very familiar with. And we know their thermal properties, so we know how they work. There are like you said, we mentioned Rondo with the bricks battery, but there are also companies producing batteries made of cement or materials similar to cement. So, this is absolutely doable.
Michael Liebreich Now what do you say... I've got a friend who is working on using hydrogen in brick kilns, brick firing, making bricks. And she says electrification just wouldn't work. You couldn't raise the temperature because it's not just a question of the temperature, it's the speed at which you get to that temperature, which actually affects the quality of the bricks. So, it's the profile of how fast you heat and how fast or slow you reduce the temperature. What do you say to her? If she says you can't do that electrically? Is that what you found?
Dr Silvia Madeddu But to be honest, the speed to which a furnace would heat, this is news to me that it's so slow, I would think that actually it's faster. So, this is news to me. But what I want to say... this might be a case of, well, first of all, hydrogen combustion to supply heat is something that should only come where there is no other alternative, and direct electrification for supplying heat with furnaces exists as an option. Now the question is, help the ceramic industry develop the needed experience to optimize these electric furnaces, for heating up bricks at the temperatures that they need, or other types of ceramic. Because you know, the transferability of a technology, it's not so trivial. I mean, it can be that you need to optimize that process. You need to find the right design of the furnace, for example, so that the heat gets delivered directly to the materials and doesn't get lost. You might need to cover your furnace, to line your furnace with different materials so that you have lower heat loss, and so on and so forth. There are many aspects, in my opinion, sometimes. So maybe this friend of yours, she's right, she didn't find the right furnace. But the problem is, I don't think it's a lack of existing technology. It's a lack of developed expertise in optimizing that technology design for the purpose that she needs, which is to eat up ceramics.
Michael Liebreich And when you talk to corporates, and when you talk to governments, do you find them on board with this? Because it feels to me like a huge opportunity. If nobody's making a furnace to make bricks electrically, that feels like it'd be a huge advantage, a huge competitive opportunity. Because if you're the first furnace maker who masters this, and who can deliver them, and you can optimize, surely the next... the story of the coming decades is going to be: if that's the technology direction, if that's more efficient, if that's lower cost, if that's cleaner, if that's better for air quality, don't you win?
Dr Silvia Madeddu You touch on a very, very important point, which is, in my opinion, when I spoke with companies, like manufacturers of these furnaces - this was three years ago, not now, now I think the landscape has changed - they were very, a bit I have to say... they were not aware that maybe this electrification wave was coming. So, they were asking me, ah, but do you think that actually there is a market for this? Some of them, you know, they were a bit surprised, because they were used to okay, for that market industry, I produce a gas-fired furnace, then for this other niche market, I produce the electric furnace. So, we need first of all, companies need to understand that there is a huge business opportunity here, because we are in desperate need of expertise and know-how. And we need companies that make the right design for these furnaces, that work directly in cooperation with industry, and they understand what is the need. Because I don't think it's really an engineering problem. It's really, they didn't have demand so far. But they do have the expertise, because if they want they can develop these furnaces and optimize these furnaces. And we saw the same a bit with heat pumps, right? I mean, the problem with heat pumps is that for many years, industry was a bit reluctant in implementing heat pumps, because they were okay, this is a new technology, something that we are not used to use, and they needed the expertise that engineers that are available in explaining and making accessible for industry that this technology can be trusted. And I think it's the same with the furnaces.
Michael Liebreich Yeah. And I want to come to your role, I promised we'd get back to your role with Schneider. Are you now moving on to the kind of electrical control of these processes side of things, or have they brought you in to kind of help to work with...? Because if you electrify a furnace, you're going to completely change the control systems, fabulous business for Schneider. Is that what you're doing? Is that what you're excited about?
Dr Silvia Madeddu So, there is definitely this opportunity. There are synergies there for sure. I have to say my role at Schneider, I'm very new to the company. So, at the moment I'm part of the sustainability business team so my role is to really, for example, advise companies in what could be the best practice to lower their carbon footprint. So, this is my role at the moment. I see huge synergies of course in the electrification of industry and what Schneider does, because they produce automation systems smart, management of energy demand, efficiency measures. So, you know, it has a lot to do with electrification. But at the moment, my role is not yet that. It is more advising companies, and working directly with companies, which is very exciting for me, because, I feel like I am making a difference with my role, I'm directly working with industry stakeholders, so I'm directly advising them, and talking to them, and also understanding, for example, some of these problems when I talk to them. So, I think it's very, very stimulating.
Michael Liebreich I just really hope that we don't lose your voice, as an advocate of electrification of industrial processes, the core processes, not just an overlay of electric controls on top, but really... It just strikes me as being such an opportunity-rich area, but we do need to persuade the manufacturers of the equipment, the process equipment, that there's a market, and we need to persuade the people who are buying those processes, that this is not some weird, wonderful, new, technologically risky thing so that we do need these voices, don't we?
Dr Silvia Madeddu Absolutely. No, I agree with you. I think that also we need to still have to explain these things a bit for some time. I think we will have to do this communication role, we will have this communication role for quite some years still to come. Because, like you said, there are many misconceptions. And also, sometimes we think that these furnaces are new technologies, but furnaces have existed since forever. You know, we know these technologies very well, it's just a problem of bringing these two groups of stakeholders together, and sharing this expertise and sharing the needs also, because really, like I said, some manufacturers don't know that there is a need for these technologies. And now some of them are waking up, and I think that the first movers in this business will be the ones that will gain the most because they will have the expertise and the know-how for which we are craving. So, we are craving for this expertise. And once these companies move forward first, they will have the advantage on the markets for sure.
Michael Liebreich Well, what we'll be doing, and I certainly hope you will as well is promoting this podcast and the YouTube accompanying show. It's the same thing, we've got about 20% of people watch on YouTube and about 80% on the podcast. And we'll be using it to get this message out there that industry can, up to 99% of its heat demand, meet it through direct electrification. So, if we can play a little bit of a role in continuing to prod that discussion, then I'll be very pleased and proud.
Dr Silvia Madeddu Absolutely, absolutely. I mean, I'm always advocating for electrification. So, for sure, I will do my part in this.
Michael Liebreich Very good. Silvia we're pretty much out of time, I'd like to thank you on behalf of our audience for joining me here today. And it's been incredibly enlightening, and it's an optimistic message, the huge opportunity. So, thank you very much for sharing that with us.
Dr Silvia Madeddu No thank you Michael for inviting me, it was a pleasure. I will certainly also advocate about the podcast you're making, you're producing, the YouTube videos. And I think that it's a great opportunity, it's a great platform that you give us to share our expertise and our knowledge and I really thank you and I will definitely promote this. And thank you so much for your role in sharing the information.
Michael Liebreich Very good. So, goodbye. Thanks for joining us.
Dr Silvia Madeddu Thank you, Michael. Bye. Bye bye.
Michael Liebreich So, that was Dr. Silvia Madeddu, now Senior Sustainability Consultant with Schneider Electric, but also one of the world's great authorities on the decarbonisation of industry. Now, next week is going to be a special episode of Cleaning Up, it'll be the audio version of my most recent piece for BloombergNEF, and it'll be on Russia's war on Ukraine, the impacts, and how I think it's going to give way to the great clean energy acceleration. Please join me this time next week for an audioblog version of Cleaning Up. Cleaning Up is brought to you by Capricorn Investment Group, the Liebreich Foundation and the Gilardini Foundation.